Case Studies
Home | Case Studies |Large Scale Subsea Project
CASE STUDY 7:
Large Scale Subsea Project
Project Specification
HCS were delighted to be invited to work with a major client on a large-scale project. This project involved manufacturing, assembling, and testing 3 x SSIV units, 14 x CDA units, 2 x DUTA units, and 2 x manifolds.
We undertook the project over two years on the client’s site. The size and scale of this project tested our project management and quality control processes as well demonstrating both our engineering talent and experience in delivering large scale subsea projects.
The detailed work scope demanded a highly collaborative working partnership between HCS and the client’s internal teams.
Our Delivery
Our first step was to appoint a core project team involved in the delivery over a two year period. The team consisted of functional experts from across our business but primarily projects, quality and operations.
The validation of new weld procedures was a priority undertaken by our quality team with the support of our welding engineer and technicians proficient in working with inconel 625, 6mo, duplex, super duplex and hastelloy c276.
Initially, the project team worked five days a week on-site. However, as the project scaled up, construction split across two sites operating a 7 day/12-hour shift schedule. HCS appointed additional technical staff to accommodate the increased working hours and additional personnel to support the core project team.
Midway through the project, HCS were asked by the client to commit further resources to support another aspect of the project. Two additional welder/pipefitter crews were appointed and supported by another NDT inspector.
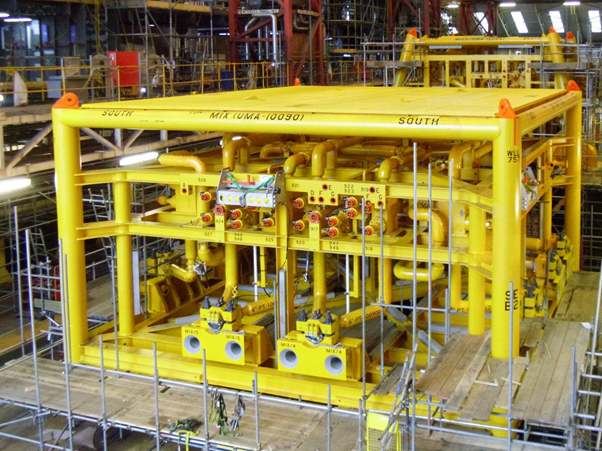
The Result
This project evidenced our capability to deliver quality product engineering excellence and workmanship. It highlighted our quality management and project management expertise. The project also showcased our efforts to adapt to the resource required to fulfil the project timescales and client expectations.
All HCS input helped to meet the client’s project timeline throughout the two years. Our contribution to this project involved over 5,000 orbital welds – 100% NDT and pressure tested.
Key elements of the project specification included:
- A total of 80,000 labour and management man-hours over 2 years.
- A total of 73 project variations we overcame.
- We provided 282 evidenced invoices for the client’s auditors.
- 12 weld procedures were developed and qualified.